¿Quien dijo que la estadística es aburrida y no sirve para nada? Bueno, lo de aburrida puedo entenderlo y dependerá de cada uno, pero su importancia en multitud de ámbitos es indiscutible.
En nuestro post sobre Mejora Continua mencionábamos a los gráficos de control como una de las herramientas básicas. Fue una de las primeras en ser aplicadas en la industria de automoción. ¿Has oído hablar de ellos? ¿Sabes utilizarlos? Si no es así, te invito a que sigas leyendo, y no te preocupes, prometo no poner más que dos o tres fórmulas estadísticas…
El nacimiento de una gran herramienta
Fue durante la década de 1920 cuando Walter A. Shewhart ideó el concepto de Gráfico de Control, mientras trabajaba para la empresa estadounidense Bell Labs. Impulsado por el afán de reducir los fallos en los sistemas de transmisión telefónicos, Shewhart y sus compañeros tenían claro que dicha mejora pasaba por reducir la variación de los procesos de fabricación de dichos sistemas, causados por causas comunes y causas especiales. Teniendo las causas comunes controladas, serían capaces de mejorar el proceso eficientemente y con ello reducir los problemas de calidad posteriores.
Posteriormente, las teorías e ideas de Shewhart llegaron a manos de W. Edwards Deming, quien se encargó de su desarrollo, extensión y aplicación a lo largo y ancho de la industria japonesa y estadounidense durante todo el siglo XX.
Configuración e Interpretación de los Gráficos de Control
Dado que existe una gran cantidad de información detallada y textos especializados sobre estas y otras herramientas de mejora, trataré de explicarlo de una forma básica y entendible, evitando entrar en detalles estadísticos o matemáticos demasiado profundos, con el objeto de hacer más ameno el post.
Los gráficos de control tratan básicamente de informarnos sobre la estabilidad y variabilidad de un proceso, generalmente aplicado en procesos de fabricación, de ahí su importancia en la industria de automoción. Y su función es ayudar a identificar las causas especiales de dicha variabilidad, para poder controlarla y finalmente eliminarla.
Existen diferentes tipos de gráficos de control, dependiendo de si se miden datos por variables o por atributos, y en función de las variables que se quieran controlar (x-S, x-R,…).

Fuente: http://www.isixsigma.com
Básicamente dichos gráficos consisten en dos ejes de coordenadas donde en el eje vertical representa la medida, variable o atributo que queramos controlar a lo largo del tiempo o del n° de muestras, que será representado en el eje horizontal.
Al gráfico se le añadirán tres líneas horizontales, una correspondiente al Límite de Control Superior (LCS), otra como Límite de Control Inferior (LCI) y otra que represente el valor nominal de nuestra medida o la media. La distancia entre los límites será de ±3σ, siendo σ la desviación típica de la muestra, partiendo de la base de que la mayoría de procesos se adaptan a una distribución normal gaussiana.
Representando los puntos correspondientes de la medición de cada muestra se obtendrá una visión general de la tendencia, la variabilidad y la estabilidad de nuestro proceso. Por regla general, la variabilidad de los puntos que no se salgan de los límites fijados será debida a causas comunes o intrínsecas al proceso, predecible y sobre la que no podremos actuar a no ser que mejoremos el sistema global del proceso. Dicha variación deberá ser irregular, aleatoria, sin tendencia alguna, en caso contrario, estaremos ante un proceso inestable. De igual forma, los valores deben estar dispersos en torno al valor central o media, si no es así, será necesario ajustar los parámetros del proceso para que quede centrado.
Sin embargo, los puntos aislados que caigan fuera de los límites fijados serán debidos a causas especiales de variación, impredecibles, y serán sobre los que deberemos prestar atención para eliminar sus causas y poder estabilizar el proceso.
En caso de que varios puntos caigan fuera de los límites puede indicar que el proceso es caótico, inestable e incontrolado, y en ese caso es posible que necesitemos herramientas más avanzadas para poder analizarlo más en profundidad, por lo que una buena interpretación del gráfico es esencial.
A continuación os dejo un par de documentos donde se explica con más detalles dichos gráficos, cómo fijar los límites de control y algunos ejemplos sencillos:
- Gráficos de Control por Atributos
- Gráficos de Control por Variables (1)
- Gráficos de Control por Variables (2)
Aplicación al Control Estadístico de Procesos
La aplicación por excelencia de los Gráficos de Control es en el ámbito del Control Estadístico de Procesos (SPC por sus siglas en inglés).
El Control Estadístico de Procesos es una de las herramientas de calidad básicas y más extendidas en el ámbito productivo como forma de controlar y medir la variabilidad de los procesos, y se sirve a su vez de los Gráficos de Control como herramienta de análisis.
Para saber si un proceso es estable o no, deberemos adentrarnos en el concepto de Capacidad de Proceso. Suponiendo que tenemos un proceso (ajustado a una distribución normal) sin causas especiales de variabilidad presentes, entonces el 99,73% de las muestras estarán entre µ±3σ, siendo µ la media y σ la desviación típica. En este caso diremos que 6σ es la variabilidad intrínseca del proceso, también llamada Capacidad del Proceso, y que viene representada por la anchura de la campana de Gauss del proceso.
A raíz del concepto de capacidad, surgen otros parámetros como los índices Cp, Cpk,…, que relacionan la capacidad de los procesos con la amplitud de los límites o tolerancias.
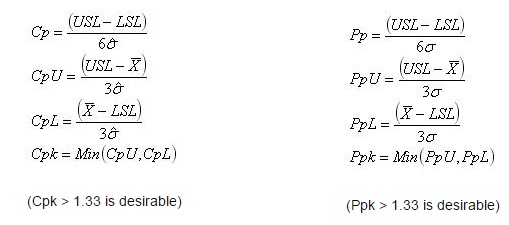
Fuente: http://www.qimacros.co
El indicador Cpk tiene en cuenta si el proceso está centrado o no, por lo que es más representativo que el Cp. En este caso diremos que un proceso es capaz si su Cpk>1. A pesar de esto, hoy en día en la industria de automoción se suele exigir un Cpk>1,33, fijándose como objetivo ideal a conseguir un Cpk=2, que se correspondería con un proceso de capacidad 6 sigma (3,4 defectos por millón de eventos).

Fuente: http://www.cqeweb.com
Los índices Pp y Ppk (Process Performance Index) también indican la capacidad de proceso, aunque se diferencian en la desviación estándar que se utiliza para su cálculo. Cp y Cpk utilizan la desviación estándar de una misma muestra, es decir, considera únicamente la variabilidad inherente al proceso a corto plazo. Mientras que Pp y Ppk utilizan la variabilidad total, tanto por causas comunes como por causas especiales, considerando el largo plazo. No pretendo entrar a los detalles estadísticos que diferencian un índice de otro, por lo que tomaré como referencia el indice Cpk.
De forma análoga, si lo que se quiere analizar es la capacidad de una máquina específica del proceso, entonces tendremos los índices Cm y Cmk.
Para aquellos que os quedéis con ganas de entrar más en detalle sobre este tema, os recomiendo echar un vistazo a los Apuntes de Análisis Estadístico de Procesos elaborados por la Universidad Pontificia de Comillas, los cuales me han parecido muy didácticos y completos.
Una vez que conocemos los parámetros de capacidad, y con ayuda de los gráficos de control, estaremos en disposición de analizar si nuestro proceso es estable o no. Hoy en día todo este análisis es realizado por programas informáticos específicos, en muchas ocasiones directamente instalados en las máquinas del proceso y capaces de generar resultados en tiempo real. No obstante, su correcta interpretación queda en manos de las personas, de las cuales depende que el proceso llegue a ser estable o no.
He aquí un ejemplo de la interfaz que suelen tener este tipo de softwares y de la información que se visualiza en ellos:
Espero haberos ayudado a comprender las bases de lo que son los gráficos de control, su importancia y su aplicación en la industria, especialmente en la de automoción, donde estas herramientas son utilizadas a diario. Recordad que todo proceso tiene variabilidad, forma parte de su existencia, y lo importante es averiguar sus causas, tenerla controlada y poder actuar sobre ella cuando sea necesario.
Este artículo es muy claro e ilustrativo. Si quereis profundizar mas sobre el control estadistico y os interesa conocoer que es CpK, os recomiendo este artículo: http://www.measurecontrol.com/que-es-cpk/
Me gustaMe gusta